Top Guidelines Of Alcast Company
Table of ContentsNot known Facts About Alcast CompanyThe Only Guide for Alcast CompanyHow Alcast Company can Save You Time, Stress, and Money.Some Ideas on Alcast Company You Need To KnowHow Alcast Company can Save You Time, Stress, and Money.Our Alcast Company Diaries
The subtle difference hinges on the chemical web content. Chemical Contrast of Cast Aluminum Alloys Silicon promotes castability by decreasing the alloy's melting temperature level and boosting fluidness throughout spreading. It plays a vital function in permitting intricate mold and mildews to be loaded accurately. In addition, silicon contributes to the alloy's stamina and put on resistance, making it important in applications where toughness is crucial, such as automobile parts and engine components.It also enhances the machinability of the alloy, making it easier to refine into finished items. This way, iron adds to the total workability of aluminum alloys. Copper boosts electric conductivity, making it advantageous in electric applications. It additionally improves deterioration resistance and contributes to the alloy's total toughness.
Manganese adds to the stamina of light weight aluminum alloys and enhances workability (Casting Foundry). It is generally utilized in functioned aluminum items like sheets, extrusions, and profiles. The visibility of manganese aids in the alloy's formability and resistance to fracturing during manufacture processes. Magnesium is a light-weight aspect that provides stamina and impact resistance to light weight aluminum alloys.
The 9-Minute Rule for Alcast Company
Zinc improves the castability of light weight aluminum alloys and assists regulate the solidification procedure during casting. It improves the alloy's stamina and solidity.
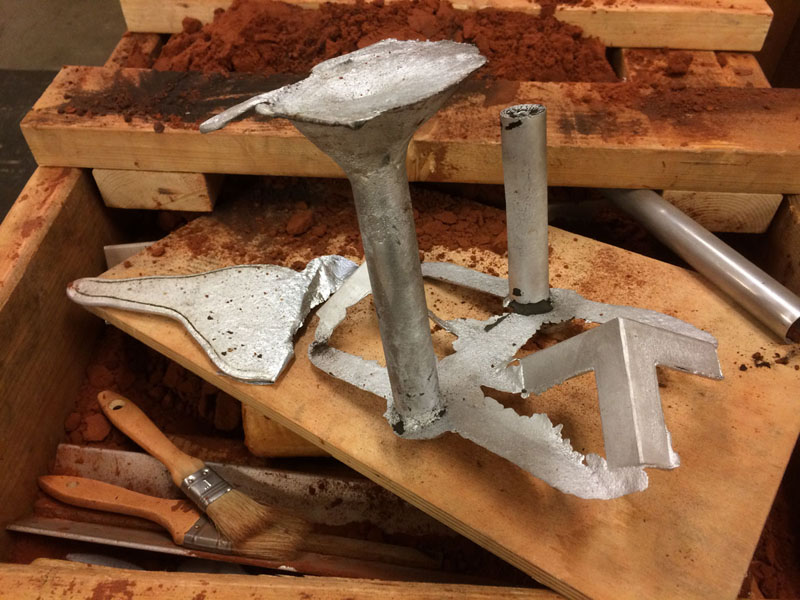
The key thermal conductivity, tensile toughness, yield strength, and elongation differ. Select suitable resources according to the performance of the target product produced. Among the above alloys, A356 has the greatest thermal conductivity, and A380 and ADC12 have the least expensive. The tensile restriction is the contrary. A360 has the best return toughness and the highest elongation price.
Indicators on Alcast Company You Should Know

In precision casting, 6063 is fit for applications where intricate geometries and top notch surface finishes are vital. Instances include telecommunication rooms, where the alloy's exceptional formability permits sleek and visually pleasing layouts while maintaining structural integrity. Likewise, in the Lights Solutions industry, precision-cast 6063 components create sophisticated and reliable lights components that require complex shapes and good thermal performance.
It leads to a better surface area coating and far better deterioration resistance in A360. In addition, the A360 exhibits YOURURL.com superior prolongation, making it ideal for complex and thin-walled components. In accuracy spreading applications, A360 is appropriate for markets such as Consumer Electronics, Telecommunication, and Power Devices. Its boosted fluidness allows for intricate, high-precision components like smart device coverings and interaction device real estates.
The Basic Principles Of Alcast Company
Its unique properties make A360 an important selection for precision casting in these markets, boosting item sturdiness and top quality. Aluminum alloy 380, or A380, is a commonly utilized spreading alloy with numerous unique attributes. It offers outstanding castability, making it an excellent choice for precision casting. A380 shows good fluidness when molten, ensuring detailed and comprehensive mold and mildews are properly reproduced.
In accuracy spreading, light weight aluminum 413 radiates in the Consumer Electronic Devices and Power Devices sectors. This alloy's remarkable corrosion resistance makes it an outstanding option for exterior applications, guaranteeing long-lasting, sturdy products in the mentioned sectors.
All about Alcast Company
Once you have actually decided that the aluminum pass away casting process appropriates for your task, a vital following step is picking one of the most ideal alloy. The aluminum alloy you choose will significantly influence both the casting process and the properties of the final product. Due to the fact that of this, you must make your decision very carefully and take an enlightened approach.
Identifying the most appropriate aluminum alloy for your application will imply evaluating a large variety of attributes. These relative alloy attributes comply with the North American Die Casting Association's guidelines, and we have actually separated them right into two classifications. The very first group addresses alloy attributes that impact the manufacturing process. The 2nd covers features influencing the residential properties of the last product.
The 15-Second Trick For Alcast Company
The alloy you choose for die spreading directly impacts several elements of the casting process, like just how simple the alloy is to function with and if it is prone to casting issues. Hot cracking, likewise referred to as solidification breaking, is a regular die casting flaw for aluminum alloys that can lead to inner or surface-level splits or splits.
Certain light weight aluminum alloys are much more at risk to warm breaking than others, and your option should consider this. Another common defect discovered in the die spreading of light weight aluminum is die soldering, which is when the cast stays with the die wall surfaces and makes ejection difficult. It can harm both the actors and the die, so you must try to find alloys with high anti-soldering properties.
Rust resistance, which is currently a remarkable quality of light weight aluminum, can vary considerably from alloy to alloy and is a necessary particular to take into consideration relying on the ecological problems your item will be subjected to (Casting Foundry). Put on resistance is an additional home typically sought in aluminum products and can set apart some alloys